デザインとサンプル
At Lebo Knitwear, we firmly believe in providing our customers with the best service. This commitment is practiced from the very beginning – every step of the design process is carefully taken care of. From CAD to sample approval and beyond, we meticulously track every detail and seek approvals to ensure the highest quality clothing for our buyers.Our aim is to provide samples in just 7 days.
SHIMA-APEXは、その豊富な経験と専門知識を生かし、基本的なパターニングとプログラミングを凌駕するデザインワークステーションを作り上げました。独自のハードウェアと専用ソフトウェアにより、SHIMA-APEXシステムは他のあらゆるデザインソリューションを凌駕します。デザインコンセプトを素早く実行するために、私たちはAPEXを3Dニッティングシミュレーションとマシンプログラミングに使用しています。これにより、デザイン、生産、店舗でのサービスを迅速に提供することができます。当社の熟練した技術者は、これらの最先端ツールを利用することができます。私たちの強力なシステムにより、希望する外観を素早く実現し、デザイン・プロセスのスピードと質を高めることができます。
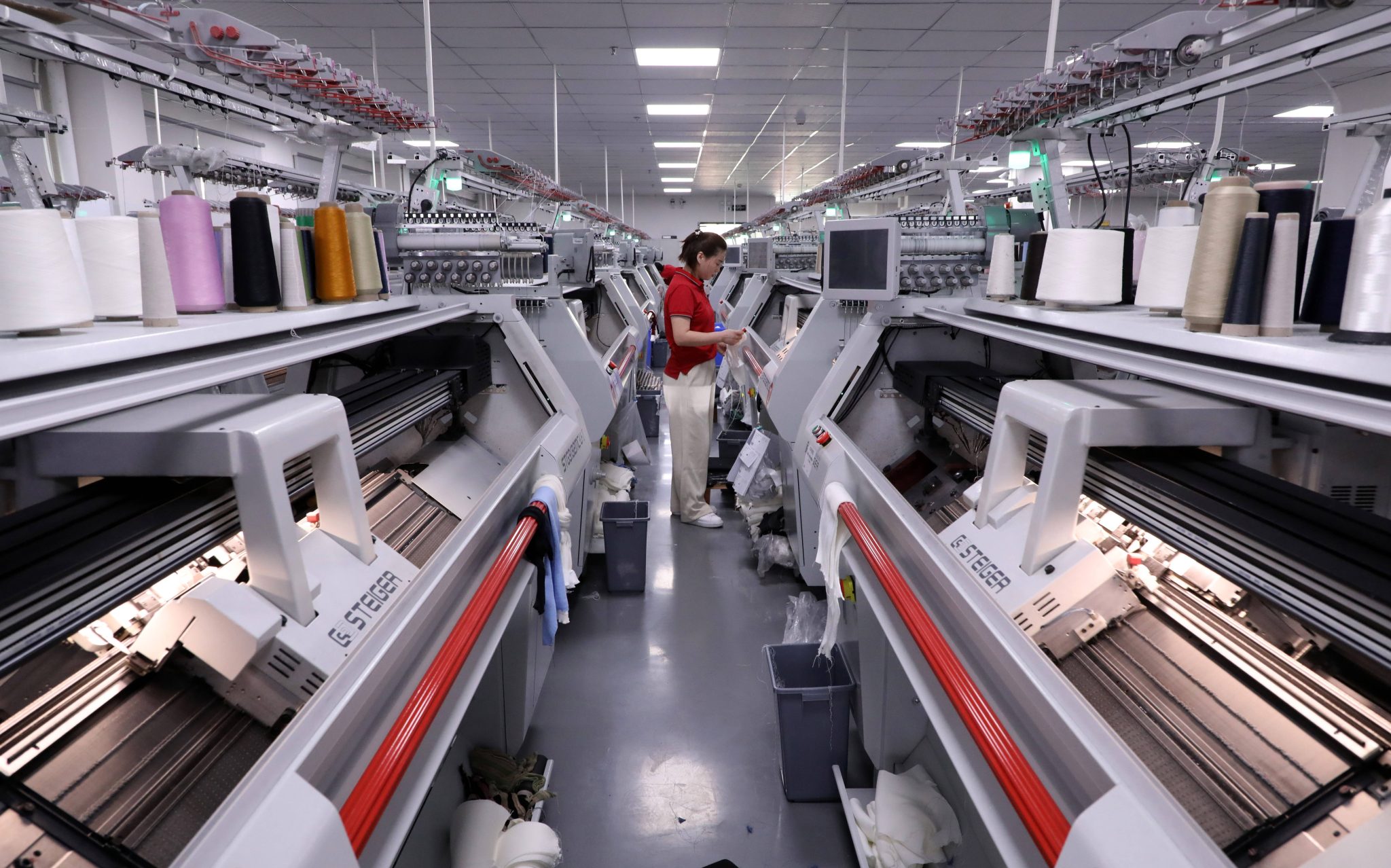
編み物
- 私たちの編み機工場は、ファッションデザインと技術力の両方を持っています。
- ゲージの範囲:1.5ggから16ggまで、様々な針ゲージのご注文に対応いたします。
- 生産能力は月産10万個。
- 当社の経験豊富な技術チームは、最も複雑なデザインやサンプルのご要望にも対応できる体制を整えています。
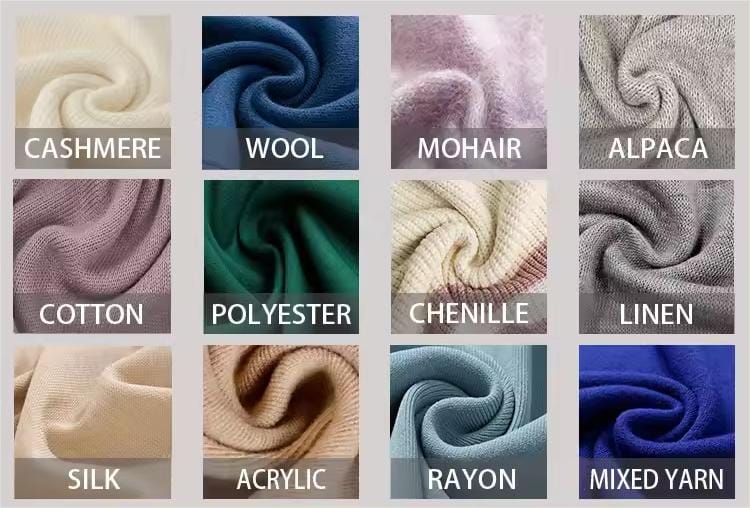
材料
We weave and then wash each kind of yarn with a particular care for the most precious ones in the world, such as ethically sourced cashmere and traceable viscose. To protect the rights and interests of consumers, giving consumers confidence that their fashion choices are environmentally responsible. We also have some other materials such as organic cotton, wool, acrylic, etc., which meet the needs of different grades of suppliers. In addition, if the quantity exceeds 300 pieces, we will provide Pantone color cards for customers to choose colors.
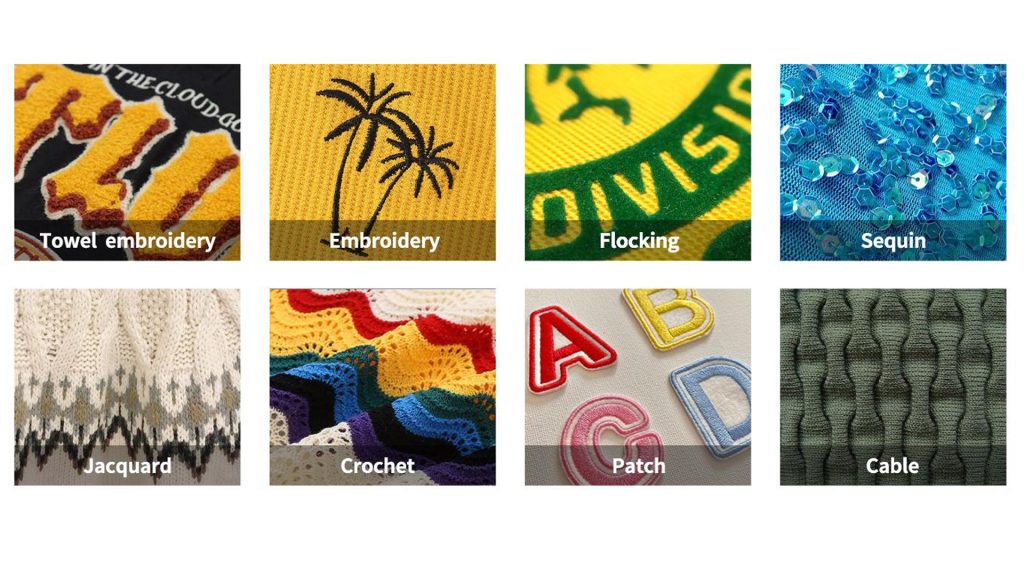
テクノロジー
セーターの職人技には、生地に独特の風合いや模様、デザインを加えるさまざまな技法がある。プリントから刺繍、ジャカードからインレイ、さらにはかぎ針編みまで、それぞれの技法は明確な創造的可能性を提供します。セーター業界で20年の経験を持つ当社は、間違いなくすべてのセーター職人技の包括的な理解を得て、当社のメーカーは、印刷、刺繍、ジャカード、インターシャ、かぎ針編みなどの専門知識を披露する高品質の製品を提供するために十分に装備されています。
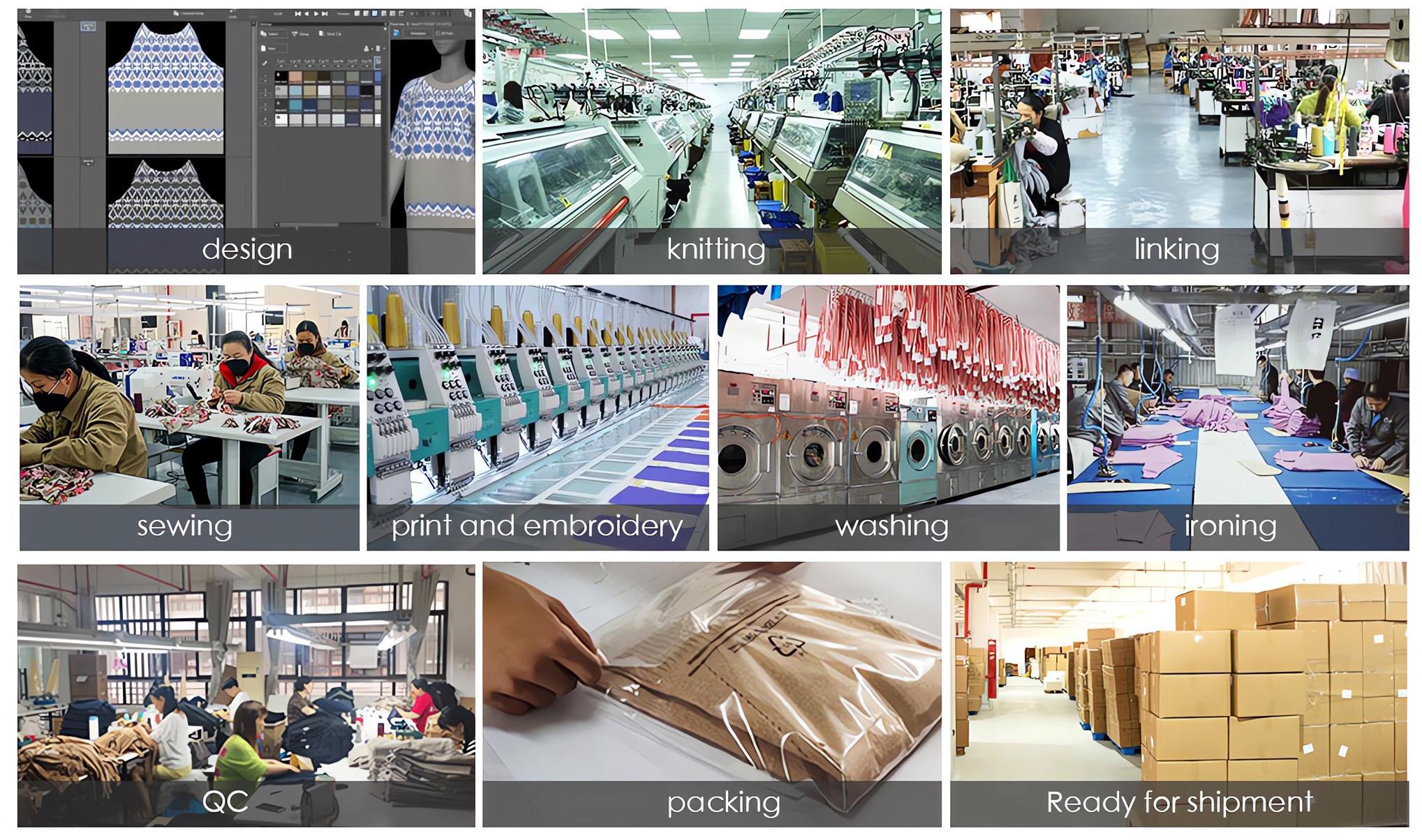
製造工程
Throughout the entire production process, strict quality control measures are in place to ensure that each sweater meets the company’s high standards. Skilled workers, machinery, and advanced technology combine to create beautifully crafted sweaters that reflect the expertise and dedication of the factory.